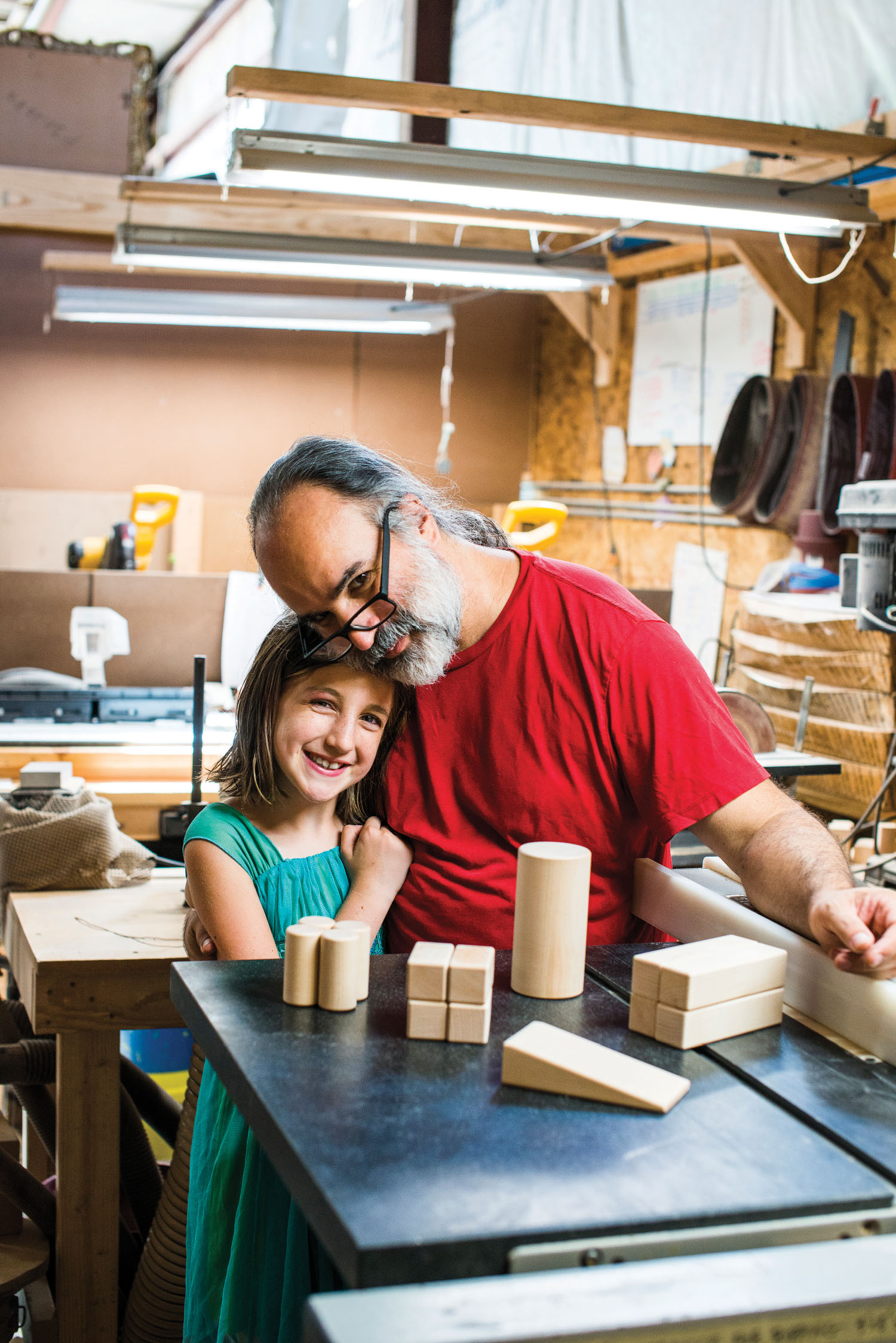
Pepi Acebo thought he might become a minister. The former Warren Wilson student spent a few years working at Unitarian Universalist retreats, including a camp in Canada. After that, he did graphic design for 15 years, but remained a man of vision.
In the spring of 2011, by then the father of a toddler daughter, Acebo once again had to figure out a way to move forward when work dried up. He considered starting a preschool co-op program. As part of that effort, he says, “I made a spreadsheet of all the different toy-block manufacturers, comparing what they had in their sets and what their costs were, so I could make the best shopping decision.” While putting this together, he ran across a website that showed how to make toy building blocks, and he decided to give it a try.
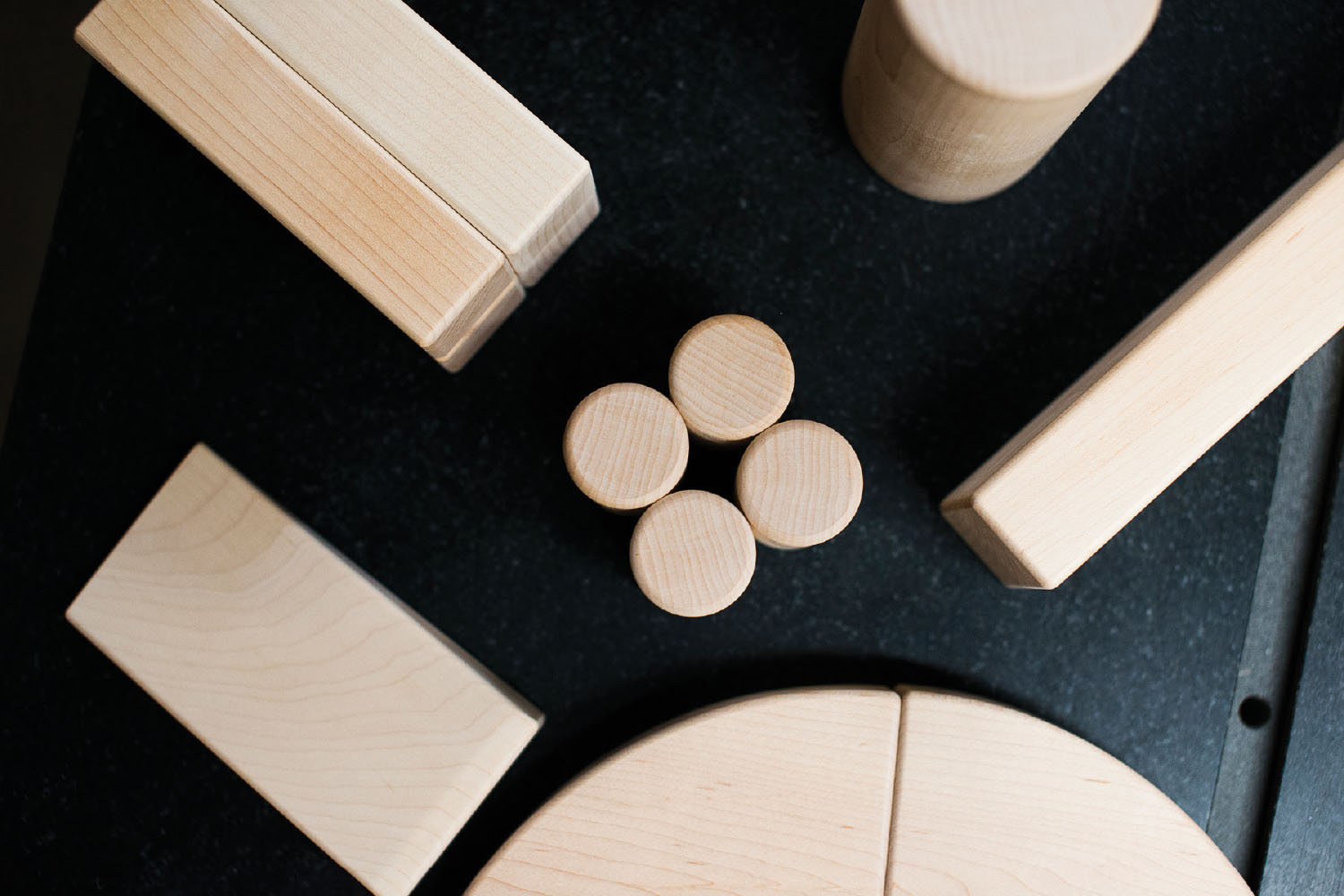
He was good at it. “I found I could make unit blocks” — wooden toy blocks cut to standardized measurements — “that were better than the ones I could buy,” says Acebo, acknowledging that he’s always had a competitive streak.
From the outset, he chose to make blocks more precisely sized (designed to a tolerance of +/- 5/1000 of an inch) than anyone else was doing. Other manufacturers’ blocks aren’t always cut to stack flush. Even a small error in the milling process can have consequences “you can see across the room — and can’t fix,” he says. “When children build with inaccurate blocks, the block building is unstable. The implicit education in mathematics and geometry is broken … it becomes more like Jenga.”
What’s more, his blocks were safer. “In hindsight, I’m somewhat appalled that I let my daughter put rubberwood blocks in her mouth,” he says, noting that even companies highly regarded for interactive educational toys, manufacture blocks with that and other tropical and subtropical hardwoods that are treated with insecticides. Acebo makes his blocks from Forest Stewardship Council-certified hard rock maple, “wood that is as close to hypoallergenic as you can get,” he claims. He rounds and smooths the blocks’ edges so they’re safe if a baby gets ahold of them.
In the fall of 2011, the maker took photos of his blocks, built a website — and dropped the idea of a preschool. “Almost immediately, people started ordering,” he says. The company is named in honor of Caroline Pratt, a progressive-education reformer who pioneered the use of wood blocks in a preschool she started in Manhattan’s West Village in the early 1900s.
Then, on the Friday following Thanksgiving that year, a story extolling the renewed popularity of using unit blocks in early-childhood education appeared on the front page of a section of The New York Times. Acebo’s orders grew accordingly.
Using a band saw and a sander in his work, he now hires assistants as needed in his 500-square-foot workshop off Patton Avenue. He says he maintains little inventory, preferring instead to make the products to fill orders as they come in. He’s shipped his blocks around the world, including fulfilling a large order from mainland China. “They’re a great tool for children to express their internalized story of the world around them.”
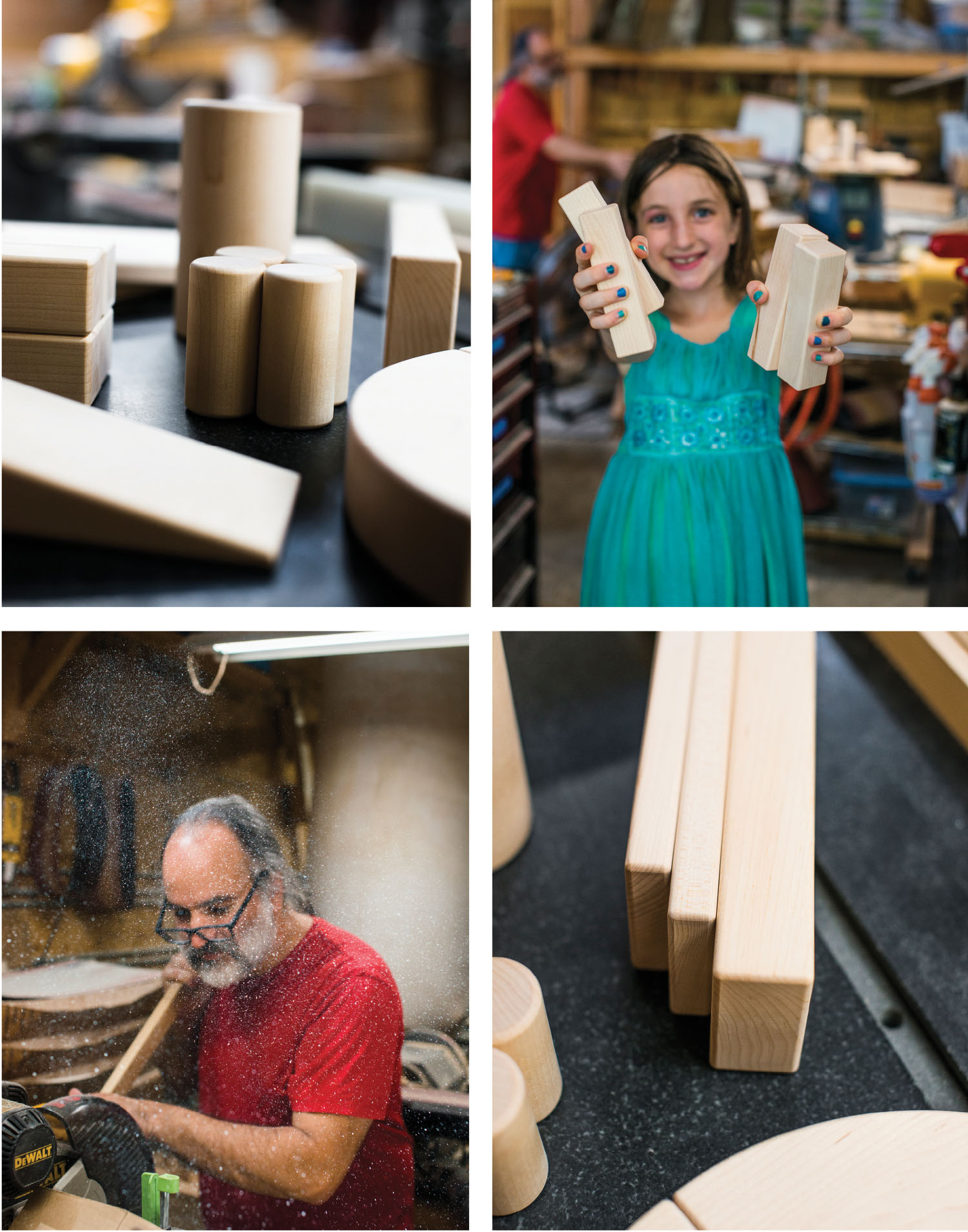
Photos by Karin Strickland
Carolina Pratt Unit Blocks, West Asheville. For more information, call 828-419-0850 or see cpunitblocks.com.