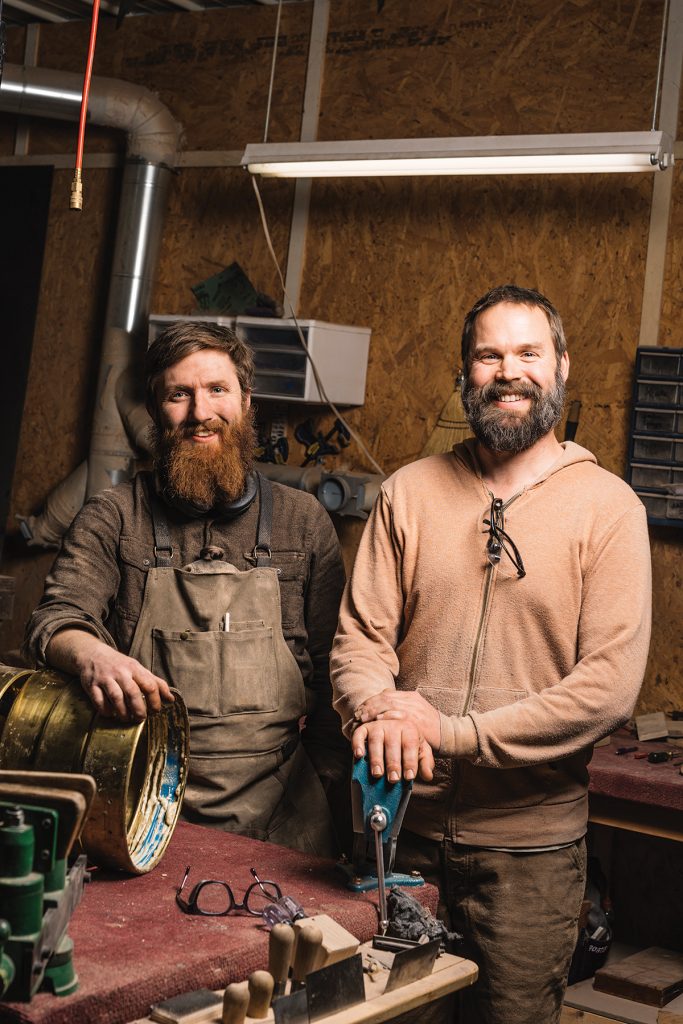
Patrick David Sawyer, left, and Adam Sacora.
Photo by Clark Hodgin
Pisgah Banjos builds handcrafted bracket-style banjos whose lineage can be traced to America’s Industrial Revolution. Founder Patrick David Sawyer and his crew of four full-time and two part-time employees use sustainable Appalachian hardwoods and materials such as Richlite, a recycled-paper and phenolic resin product mainly used for countertops, to make instruments for players of old-time music — a mountain genre that predates bluegrass (picking is generally done in the distinct “clawhammer” style).
Some are precise, exquisite reproductions of early-20th-century Vega tubaphone banjos, widely regarded as one of the best-sounding banjos ever made. Sawyer also teaches banjo-building workshops at John C. Campbell Folk School and Warren Wilson College and sells banjo-making parts worldwide.
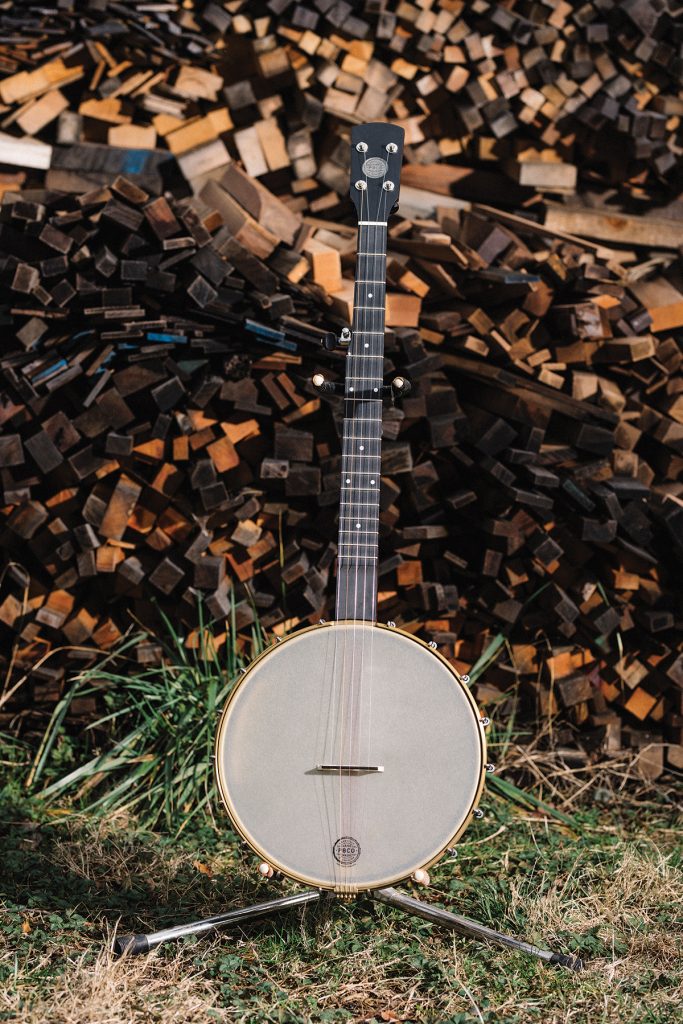
Photo by Clark Hodgin
Did you set out to run a banjo-building business?
No, I never thought I’d do this. I went to school for solar and renewable energy. In 2014, I had a really great job working for a solar company, and I enjoyed what I did.
So what happened?
Like most banjo builders, I did it part time, making banjos on weekends. But I was getting more demand for my banjos, and was traveling out of town a lot. I had a bunch of orders that I couldn’t fill quickly enough, so I suddenly had to make a choice. I bought the [Pisgah Banjo] property, a truck, and quit my job, all in the same month.
Don’t most people who make and sell banjos primarily specialize in more popular instruments, like guitars?
There are only a handful of us in the world who make banjos full time. I know that because I sell banjo parts to other builders.
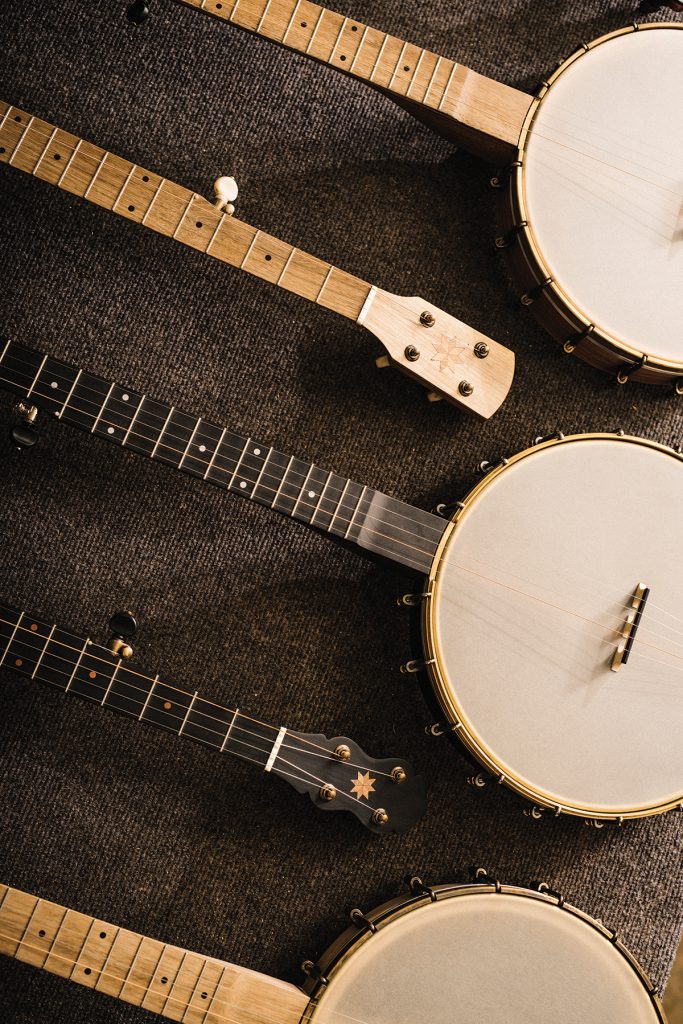
Photo by Clark Hodgin
So what’s your success formula?
I decided from the get go to be a sustainable company with a zero-waste, solar-powered facility. I’m the only banjo builder doing that, and my customers know that and like it. Also, most banjos are made overseas and just assembled here, or the manufacturing is computerized. I’m trying to recreate how they were originally made, modeling the production techniques of 100 years ago. Nobody else does that, but our banjos are still very affordable.
Antique banjos had strings made of “gut” [sometimes called “cat gut” but usually harvested from livestock]. I assume that’s not part of the revival.
We mostly use steel strings; however, we sometimes use Nylgut strings, which are synthetic strings made to mimic gut strings.
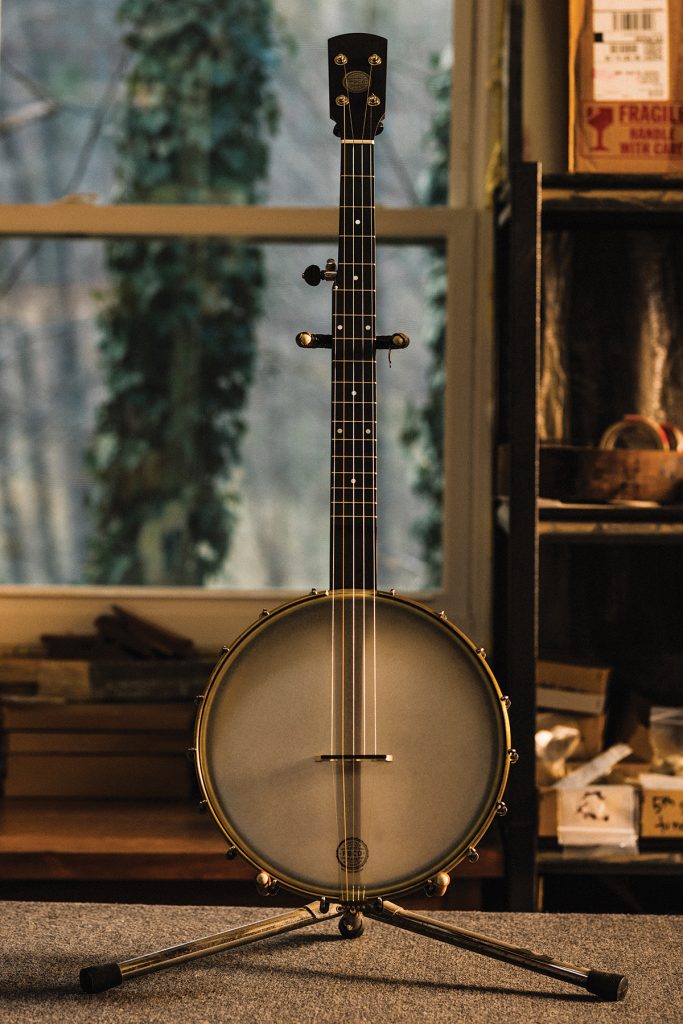
What about the tone?
Banjo tone is so subjective, and we want to build for what the customer prefers. So we have eight models and they all sound completely different. We also have a custom design tool so you can design your own. I like to tell people we can make it however you prefer and want it to sound.
How’d you learn your craft?
I started playing banjo in college, and did some woodworking with my father. Then I started researching how to build a banjo and visited a few people who knew how. One was a man who lived outside of Boone, luthier Charlie Glenn.
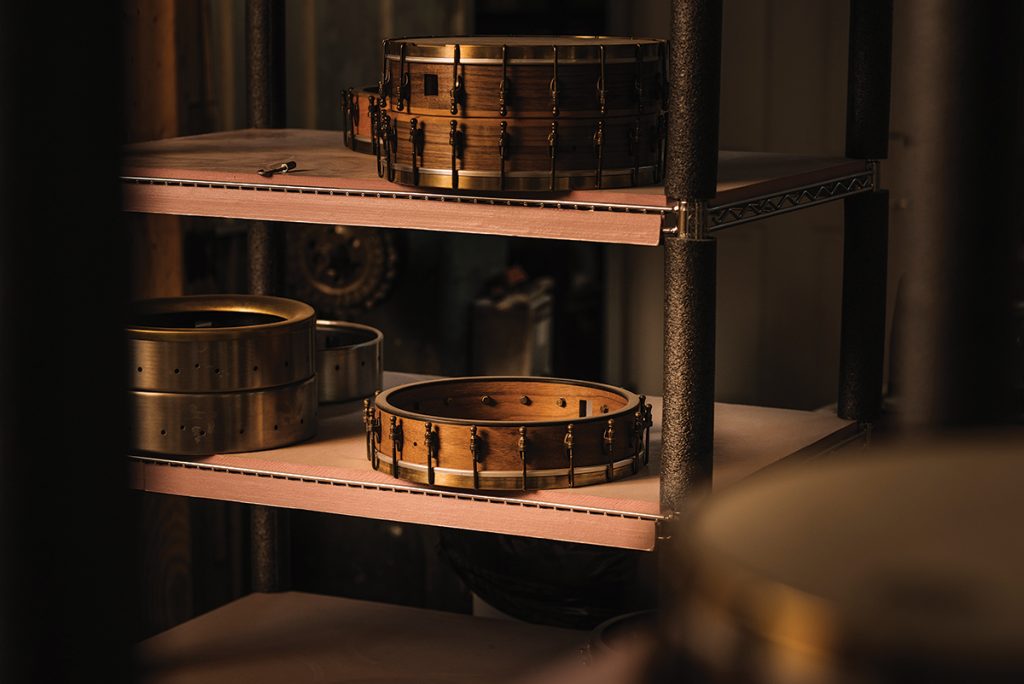
How did Charlie become your mentor?
I was working to purchase a banjo and was fascinated by what he was doing. So I asked him, “Instead of buying from you, can you teach me how to build one?
What was in it for him?
I don’t know — I think about that a lot. But I showed a lot of interest and he was just a nice dude.
Pisgah Banjos, Fairview. To learn more, or see notices of upcoming workshops, visit pisgahbanjos.com and on Instagram (@pisgahbanjos) and Facebook. Patrick David Sawyer’s banjo-parts company site is balsambanjoworks.com. Pisgah Banjos are sold locally at Acoustic Corner in Black Mountain,(105-F Montreat Road, 828- 669-5162, Acoustic Corner on Facebook).
REMINDER
.
DEAR SIR,
.
Sir we make drums heads skins and Wooden hoops.
Goat skins natural
Goat skins hair
Goat skins white
Goat skins transparent
Goat skins colour, black, red, blue, green
………
Calf skins natural
Calf skins hair
Calf skins White
Calf skins transparent
……….
Cow skins natural
Cow skins hair
………..
Buffalo skins natural
Horse skins natural
Horse skins hair
.
SIR DO YOU HAVE ANY ENQUIRERS PLEASE SEND ME. WE GIVE YOU BEST OFFER.
.
BEST REGARDS
K.A
Gold Coronet Enterprises
Nihal Chand Street Sialkot-51310-Pakistan